about davis 3p logistics
Your Trusted Partner in Streamlined Logistics Solutions
At Davis 3P Logistics, we understand that in today’s fast-paced world, efficient and reliable logistics are critical to the success of your business. With years of experience and a deep commitment to excellence, we are dedicated to providing tailored logistics solutions that streamline your supply chain and help you stay ahead of the competition. Our team of experts works tirelessly to ensure that every shipment is handled with the utmost care and precision, allowing you to focus on what you do best—growing your business. Partner with Davis 3P Logistics, and experience a seamless logistics process that delivers results.
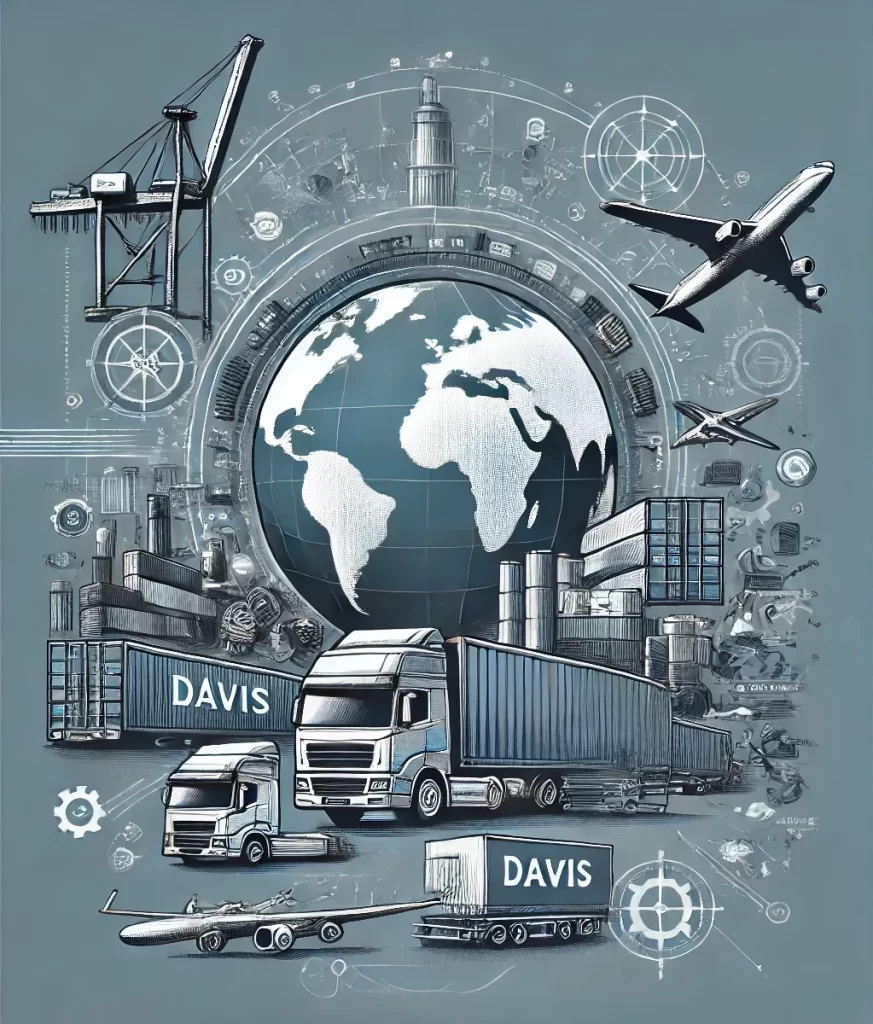
45
Countries
760+
Branches Around the World
8.5k
Deliveries Per Year
Popular Questions About our
Logistics Services
What is Logistics?
Logistics refers to the process of planning, implementing, and controlling the efficient, cost-effective flow and storage of goods, services, and related information from the point of origin to the point of consumption. It encompasses a wide range of activities, including transportation, warehousing, inventory management, order fulfillment, and distribution. The goal of logistics is to ensure that the right products reach the right place at the right time, in the desired condition, and at a competitive cost.
In today’s globalized economy, logistics plays a crucial role in ensuring that supply chains operate smoothly, allowing businesses to meet customer demands while optimizing costs. It involves coordinating and managing the movement of goods, whether by land, sea, or air, and requires careful planning and execution to minimize delays, reduce costs, and maximize efficiency.
What Does a Logistics Service Provider Broker Do?
A logistics service provider broker, often simply referred to as a freight broker or logistics broker, acts as an intermediary between shippers (companies that need to transport goods) and carriers (companies that provide transportation services). The broker’s primary role is to facilitate the shipping process by connecting these two parties and ensuring that goods are transported efficiently, safely, and at a competitive rate.
Key Responsibilities of a Logistics Broker:
Sourcing Carriers: Brokers have a network of carriers they work with. They match the specific transportation needs of the shipper with the appropriate carrier based on factors like capacity, route, and cost.
Negotiating Rates: They negotiate transportation rates between shippers and carriers to ensure competitive pricing while considering the needs and constraints of both parties.
Coordinating Shipments: Once a match is made, the broker coordinates the logistics of the shipment, including scheduling pickup and delivery times, and ensuring that all necessary documentation is in place.
Tracking and Monitoring: Brokers track the shipment from origin to destination, providing updates to the shipper and handling any issues that arise during transit.
Ensuring Compliance: They ensure that all legal and regulatory requirements are met, including customs documentation for international shipments and adherence to industry standards.
Problem Resolution: In case of delays, damages, or other issues, the broker acts as the point of contact to resolve problems and ensure that the shipment reaches its destination as intended.
By leveraging their expertise and relationships within the industry, logistics brokers help businesses streamline their shipping processes, reduce costs, and improve supply chain efficiency. They play a vital role in ensuring that goods move smoothly through the supply chain, from the manufacturer to the end consumer.
Yes, there are several different types of logistics services available, each designed to meet specific needs within the supply chain. Here are some of the most common types:
1. Inbound Logistics
- Description: Inbound logistics involves the transportation, storage, and delivery of goods coming into a business. It includes managing the supply of raw materials, components, and goods from suppliers to manufacturing or assembly plants.
- Example: A manufacturer receiving parts from various suppliers to assemble a final product.
2. Outbound Logistics
- Description: Outbound logistics refers to the process of storing, transporting, and distributing goods to the customers. This typically includes warehousing, order fulfillment, and the delivery of finished products from manufacturing plants to end consumers or retailers.
- Example: A distributor delivering finished goods from a warehouse to retail stores or directly to customers.
3. Third-Party Logistics (3PL)
- Description: Third-party logistics providers offer comprehensive logistics services, including warehousing, transportation, inventory management, and other value-added services. Companies often outsource these functions to 3PLs to focus on their core business activities.
- Example: A company hiring a 3PL provider to manage its entire supply chain, from warehousing to order fulfillment and delivery.
4. Fourth-Party Logistics (4PL)
- Description: A fourth-party logistics provider manages the logistics process on behalf of a company, overseeing multiple 3PLs. A 4PL acts as a logistics integrator, providing a single point of contact for the entire supply chain.
- Example: A large corporation outsourcing its entire logistics operation to a 4PL, which then manages multiple 3PLs and other logistics partners.
5. Reverse Logistics
- Description: Reverse logistics involves the process of returning goods from customers back to the company. This can include returns, recycling, remanufacturing, and the disposal of products.
- Example: A retailer handling returns and exchanges of products from customers, processing them for resale or proper disposal.
6. Cold Chain Logistics
- Description: Cold chain logistics involves the transportation and storage of temperature-sensitive products, such as food, pharmaceuticals, and chemicals. It requires specialized equipment and processes to maintain the necessary temperature throughout the supply chain.
- Example: A pharmaceutical company shipping vaccines that must be kept at a specific temperature range.
7. E-commerce Logistics
- Description: E-commerce logistics focuses on the specific needs of online retailers, including order fulfillment, warehousing, and last-mile delivery services tailored to the fast-paced nature of online sales.
- Example: An online retailer using a logistics provider to manage inventory, pack orders, and handle shipping to customers.
8. Freight Forwarding
- Description: Freight forwarding involves organizing the transportation of goods from one point to another, typically across international borders. Freight forwarders coordinate with various carriers, manage customs clearance, and ensure the efficient movement of goods.
- Example: A company shipping products internationally using a freight forwarder to handle customs, shipping documents, and transportation.
These different types of logistics services cater to various aspects of supply chain management, and businesses may choose one or more depending on their specific logistics needs.
Logistics providers manage supply chain risks through a combination of strategic planning, technology, and operational best practices. Here’s how they typically address these challenges:
1. Risk Assessment and Mitigation Planning
- Risk Identification: Logistics providers first identify potential risks within the supply chain, such as natural disasters, political instability, supplier failures, or transportation disruptions.
- Mitigation Strategies: Once risks are identified, they develop mitigation strategies, such as diversifying suppliers, establishing alternative routes, and maintaining safety stock to buffer against supply chain disruptions.
2. Technology and Data Analytics
- Real-Time Monitoring: Using advanced technology like GPS tracking, Internet of Things (IoT) devices, and real-time monitoring systems, logistics providers can track shipments and anticipate potential disruptions.
- Predictive Analytics: Data analytics tools allow providers to analyze historical data and forecast potential risks, helping them to proactively address issues before they impact the supply chain.
3. Supplier and Carrier Diversification
- Multiple Suppliers: To reduce dependency on a single source, logistics providers often work with multiple suppliers and carriers. This diversification helps to ensure continuity in case one supplier or route becomes unavailable.
- Carrier Relationships: Building strong relationships with multiple carriers gives logistics providers more flexibility to switch routes or modes of transportation if necessary.
4. Supply Chain Visibility
- End-to-End Visibility: Implementing systems that provide end-to-end visibility of the supply chain allows logistics providers to quickly identify and respond to disruptions.
- Collaborative Platforms: Using collaborative platforms where all stakeholders can share information helps improve communication and decision-making in real-time, further reducing the impact of risks.
5. Contingency Planning
- Emergency Response Plans: Logistics providers develop and regularly update contingency plans that outline specific steps to take in the event of a supply chain disruption. These plans include alternative suppliers, routes, and transportation methods.
- Simulation and Drills: Some logistics companies conduct simulations and drills to test their contingency plans, ensuring that their teams are prepared to respond quickly to any unforeseen events.
6. Compliance and Security Measures
- Regulatory Compliance: Ensuring that all aspects of the supply chain comply with relevant regulations reduces the risk of legal issues and delays.
- Security Protocols: Implementing robust security measures, such as cargo tracking, secure facilities, and anti-theft protocols, helps protect against theft, fraud, and other security-related risks.
7. Insurance
- Risk Transfer: Logistics providers often purchase insurance to cover potential losses from supply chain disruptions. This can include cargo insurance, liability insurance, and business interruption insurance, providing financial protection in the event of significant disruptions.
Conclusion:
By combining these strategies, logistics providers can effectively manage supply chain risks, ensuring that goods are delivered on time and within budget despite the challenges that may arise. The goal is to create a resilient supply chain that can adapt to and overcome disruptions with minimal impact on operations.
Choosing the right logistics partner is crucial for the success of your supply chain and overall business operations. Here are the key factors you should consider:
1. Experience and Expertise
- Industry Experience: Look for a logistics partner with a proven track record in your industry. Their familiarity with industry-specific challenges and regulations can ensure smoother operations.
- Specialization: Determine if they have expertise in specific logistics services you need, such as cold chain management, e-commerce fulfillment, or international shipping.
2. Range of Services
- Comprehensive Services: Ideally, your logistics partner should offer a wide range of services, including warehousing, transportation, freight forwarding, and inventory management. This allows you to consolidate your logistics needs with one provider.
- Scalability: Ensure they can scale their services to match your business growth, whether you need increased capacity during peak seasons or expansion into new markets.
3. Technology and Innovation
- Tracking and Visibility: A good logistics partner should offer real-time tracking and visibility into your supply chain. This helps in monitoring shipments and managing any potential disruptions.
- Automation and Data Analytics: Look for partners who leverage automation and data analytics to optimize logistics processes, reduce costs, and improve efficiency.
4. Geographic Coverage
- Global Reach: If your business operates internationally, ensure your logistics partner has a strong global network. This includes knowledge of international regulations, customs, and the ability to manage cross-border shipments.
- Local Expertise: For domestic operations, local expertise is vital for navigating regional regulations and ensuring timely deliveries.
5. Reputation and Reliability
- Customer Reviews and References: Research customer reviews and ask for references to gauge the reliability of the logistics partner. Consistent on-time delivery and good customer service are strong indicators of reliability.
- Industry Certifications: Certifications such as ISO 9001 (Quality Management) and ISO 14001 (Environmental Management) indicate a commitment to high standards.
6. Cost and Flexibility
- Transparent Pricing: Choose a partner that offers transparent pricing with no hidden fees. Compare costs with the services provided to ensure you’re getting value for money.
- Flexibility: Your logistics partner should be flexible in adapting to your changing needs, such as accommodating last-minute changes or handling unexpected volume surges.
7. Customer Service
- Responsiveness: Assess their responsiveness and support capabilities. A partner with excellent customer service can quickly resolve issues and provide timely updates.
- Dedicated Account Management: Some logistics partners offer dedicated account managers to oversee your operations, providing a single point of contact for all logistics-related queries.
8. Risk Management and Compliance
- Compliance: Ensure your logistics partner complies with all relevant regulations, including environmental laws, safety standards, and customs regulations.
- Risk Management: Evaluate their risk management strategies, such as contingency plans for supply chain disruptions, security protocols, and insurance coverage.
9. Sustainability Initiatives
- Environmental Responsibility: If sustainability is important to your brand, choose a logistics partner that prioritizes eco-friendly practices, such as reducing carbon emissions, using fuel-efficient vehicles, or participating in green initiatives.
Conclusion:
Selecting the right logistics partner requires careful consideration of their experience, range of services, technological capabilities, and overall reliability. By focusing on these factors, you can choose a partner that aligns with your business goals and supports your supply chain effectively.
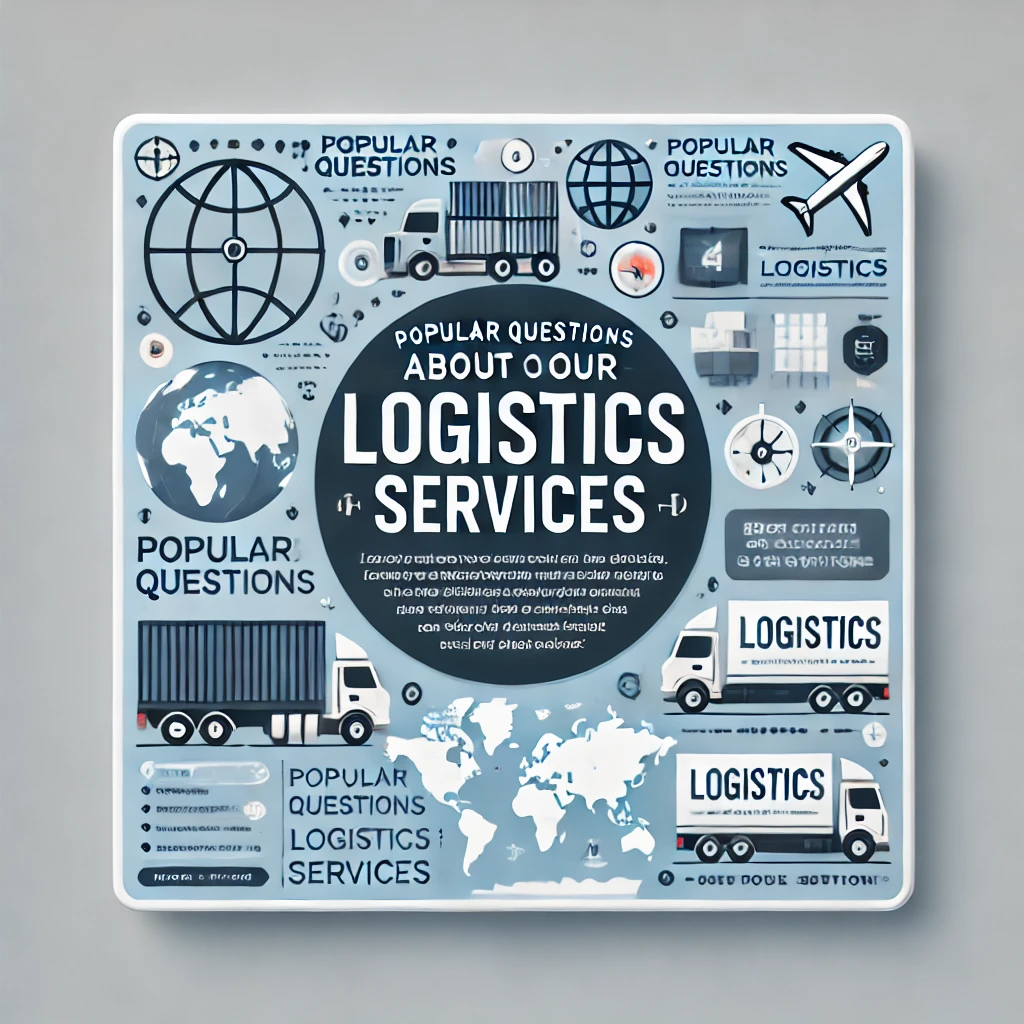